St Lukes Health – Healthiest Island on the Planet
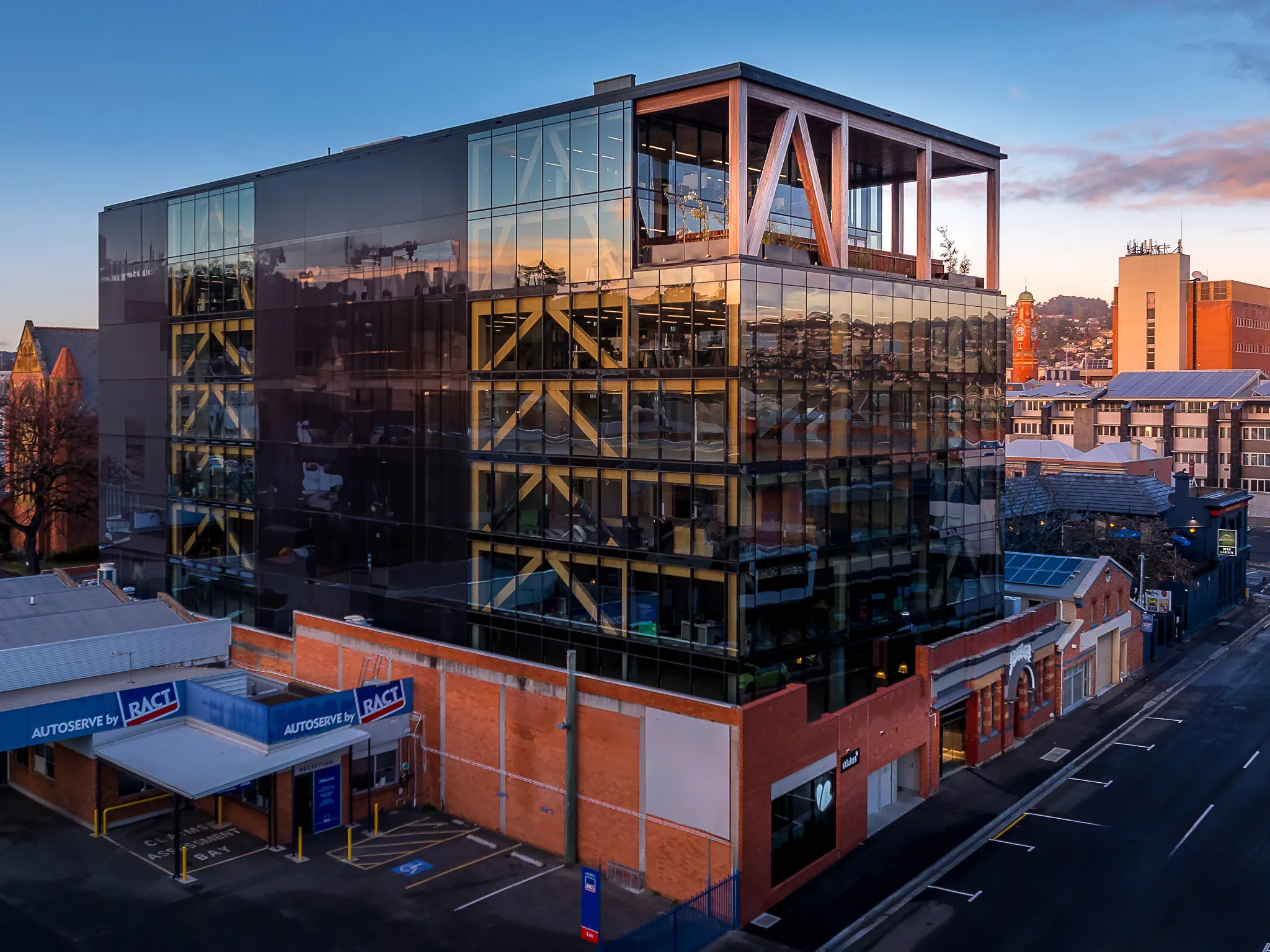
The St Lukes Health building in Launceston is the largest mass timber construction project ever completed in Tasmania. Constructed with the vision for a fit-for-purpose office space to bring together St Lukes’ workforce, the building is a new icon to the City of Launceston’s cityscape. The 30-metre, seven-storey building sets a benchmark for sustainable business practices in the region and illustrates the growing trend for environmental consideration in commercial construction. The building’s design repurposes existing heritage warehouses, integrating original timber trusses with modern mass timber construction. This approach not only enhances sustainability but also pays homage to the area’s industrial past.
The new head office stands out for the innovative construction techniques, which are so unique within the Australian market that a definitive code and set of guidelines is yet to be established for this type of build. Fairbrother’s prior experience in mass timber through projects such as ‘Galkangu’ in Bendigo provided additional confidence and understanding of the processes involved in taking on a salient project like St Lukes Launceston to completion.
“The project was always one that we targeted, given it is the largest mass timber building in Tasmania, and one of the bigger ones in the country,” said Fairbrother’s General Manager – Northern Tasmania, Marcus Perkins. “We want to be at the forefront of that specialist industry.”
The choice of mass timber was a visionary one as much as a practical decision, with the client, St Lukes Health, seeking to provide a centralised hub for their workforce who, previously, had been dispersed across four separate locations in Launceston.
“We wanted this building to be nothing short of extraordinary: visually stunning, with world-leading sustainability credentials, using Tasmanian materials and building local skills,” said St Lukes project director and board member, Martin Rees. “The project was an investment both in the health of Tasmanians, and the environment.”
The use of glue-laminated timber (GLT) and cross-laminated timber (CLT) are both significant in the construction of a project like St Lukes.
“The whole structure uses GLT and CLT in its makeup,” said Fairbrother Project Manager, Jake Herbert. “Those elements have been used in other buildings around Tasmania, but certainly this is the first multi-storey building in the state where you’re actually reliant on the timber for structure, floors, and walls.”
Prefabricated GLT and CLT components provided an opportunity for construction that outpaced more traditional concrete and steel multi-storey projects. Positive comments about the building rising at a rate of close to one level per week were received from the client throughout the construction of the building.
Whilst the initial desire was to use Tasmanian timbers and products for as much of the building as possible, the new nature of building a mass timber construction of this scale was something that required a wider look.
“We approached CUSP, based in Wynyard, to do all the CLT for the building, but their capacity is still growing,” explained Marcus. “We wanted them to supply as much as they could, so they ended up supply the CLT for the level 7 floorplate.”
CUSP’s involvement provided a significant innovation in Tasmanian timbers through the use of Eucalyptus nitens. The rapid-growing Tasmanian plantation species, typically used for woodchips, has demonstrated its worth to higher-value applications such as CLT. The material’s performance in the project has proven its viability for future mass timber constructions in Tasmania and beyond.
Sourcing the remainder of the timber materials for the build was a key logistical challenge in the planning and procurement stage. The balance of the CLT floor panels were manufactured from radiata pine, and sourced from Victoria. The GLT components were shipped from European sources, where mass timber building is far more prevalent than in Australia.
“All the GLT for the entire job fit into 12 40-foot shipping containers,” said Jake. “Basically, we got two containers a fortnight once the first container turned up. One of the things that we picked up from the Victorian guys was to make sure we had an off-site facility for these to arrive so that you can load it onto a truck and then bring it in as you need.”
Another significant challenge was meeting the fire safety requirements for mass timber buildings. Collaboration with fire engineers ensured that the building met the necessary safety standards without compromising the design. The timber’s inherent fire resistance was augmented with strategic fire safety measures, ensuring the building’s integrity and safety.
“The challenge is, under the national construction code, there’s no deemed-to-satisfy provision for mass timber,” said Marcus. “You have to get a fire engineer on board to determine what your requirements are.”
Acoustic performance was another area of focus. “Timber doesn’t perform that well acoustically compared to concrete, which is very dense. To address this, we installed raised floors with rubber backing to stop footfall transfer and enhance acoustic performance,” said Marcus.
With a lack of any universal national standard in Australia for mass timber construction, the project team relied on European standards and codes, as well as collaboration with their Victorian counterparts to ensure that the project met or exceeded quality and safety needs.
“There was actually a timber designer from Europe who was involved in the process,” said Jake. “Given the lack of standards or codes around this in Australia, realistically it was a no-brainer to engage someone with the added familiarity.”
“The next revision of the national construction code will hopefully cover more about the use of mass timber,” said Marcus. “An Australian standard will be beneficial to provide clear guidelines and facilitate more widespread adoption of mass timber as a sustainable construction method.”
Fairbrother’s approach to this project demonstrates a commitment to innovation and sustainability. The collaboration with local and international partners, combined with the use of advanced timber technology, has resulted in a building that not only meets the practical needs of the client, but also sets a new standard for sustainable construction in Tasmania.
The building contains office space for St Lukes Health staff to now have a location that brings everyone together for a more efficient and collaborative workspace. It goes beyond being an office, with the ground floor being dedicated as a wellness hub where the community can access a range of initiatives, including a St Lukes customer care centre, the organisation’s first dental practice, a cafe, and playground.
“We wanted our home to be a built manifestation of our vision to make Tasmania the healthiest island on the planet,” said St Lukes Chief Executive Officer, Paul Lupo. “We wanted the very space itself to be a motivating force that brings people together to build connections, learn ways to improve their health and wellbeing, and feel supported to take action.”
By leveraging the benefits of mass timber and showcasing innovative design and construction practices, Fairbrother and its partners have created a building that not only meets the practical needs of St Lukes Health but also embodies their vision for a healthier and more sustainable future. This project serves as a model for future developments, demonstrating that with the right vision and collaboration, sustainable construction can be both practical and inspiring.
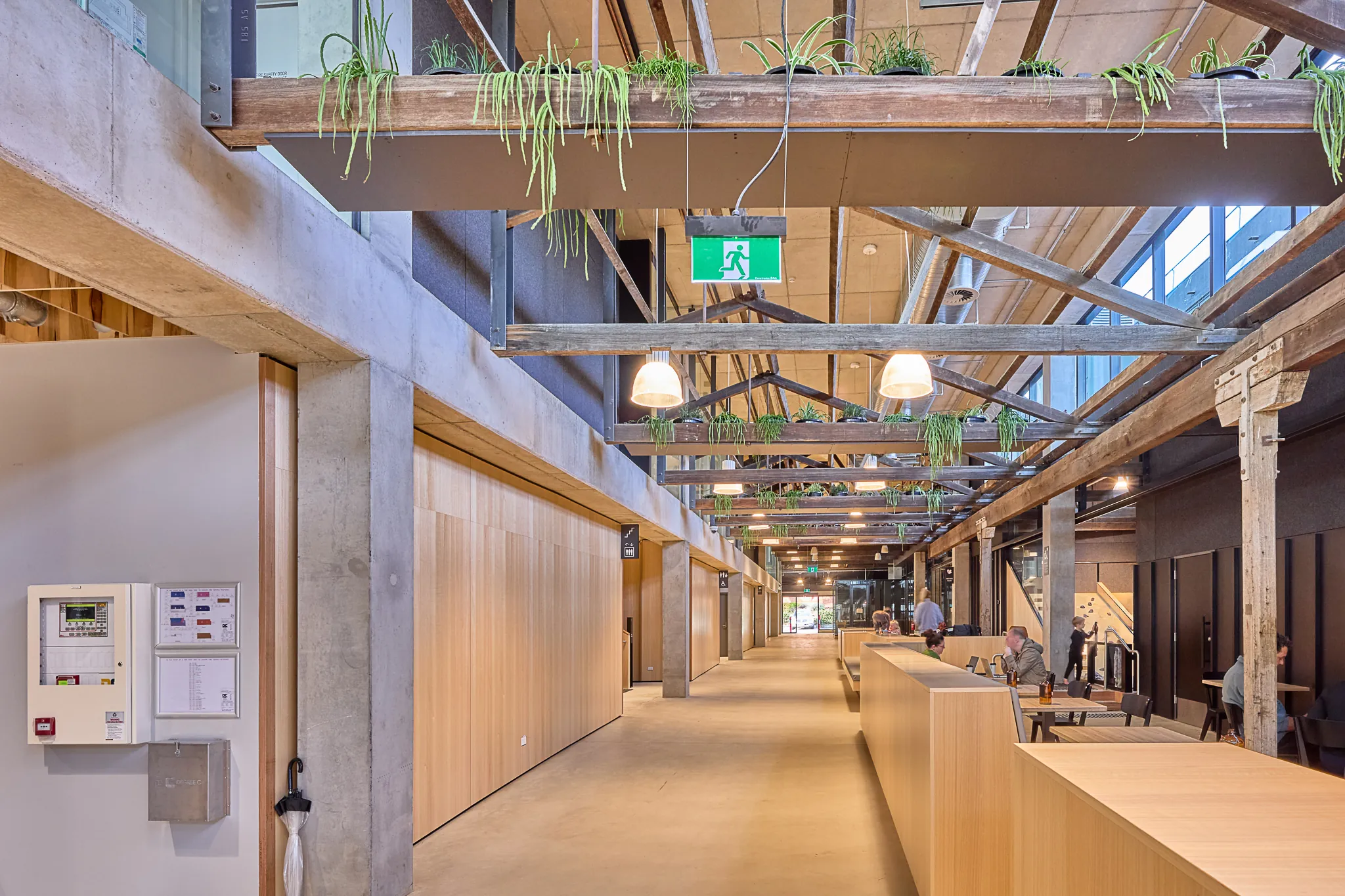
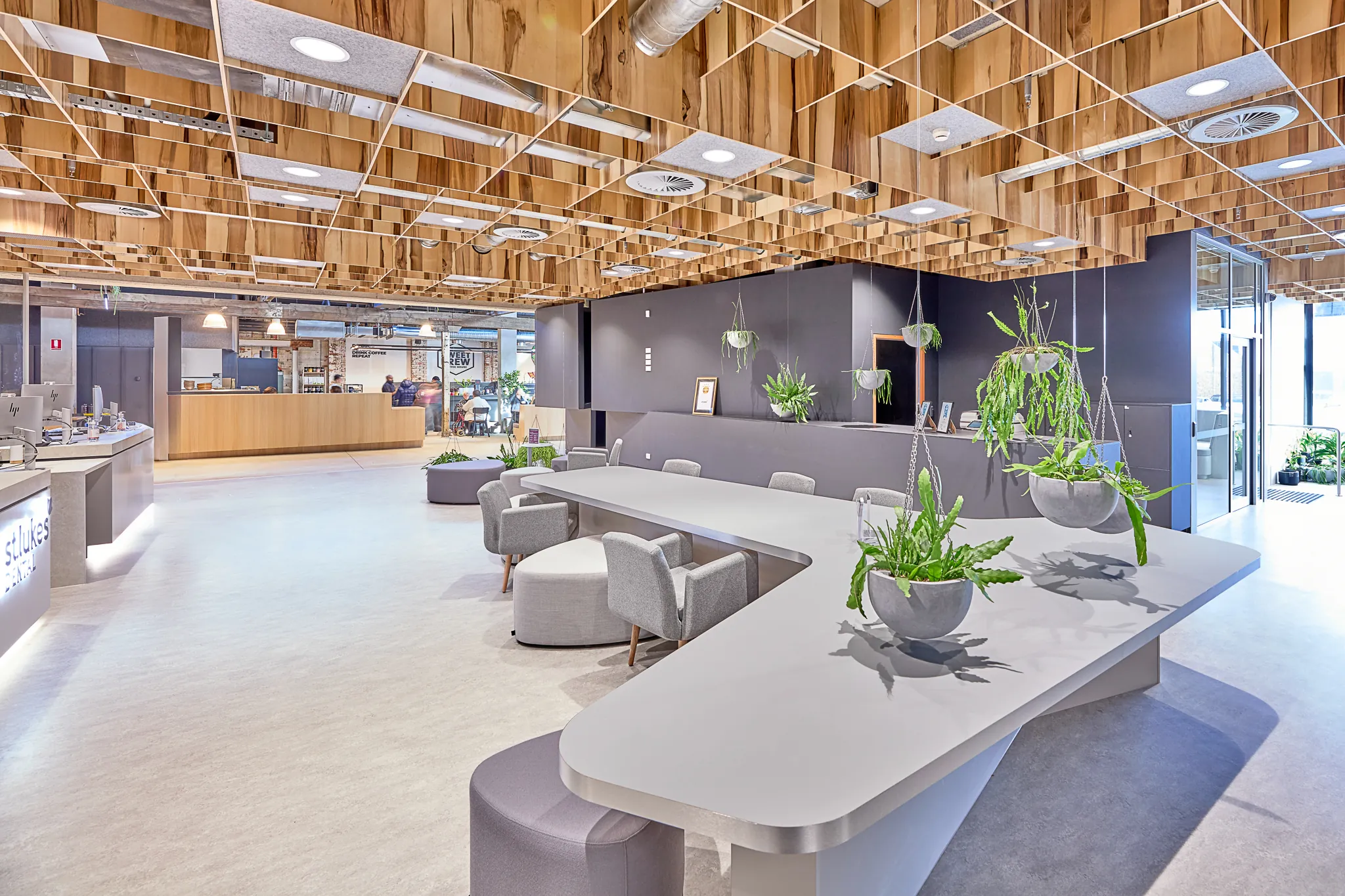
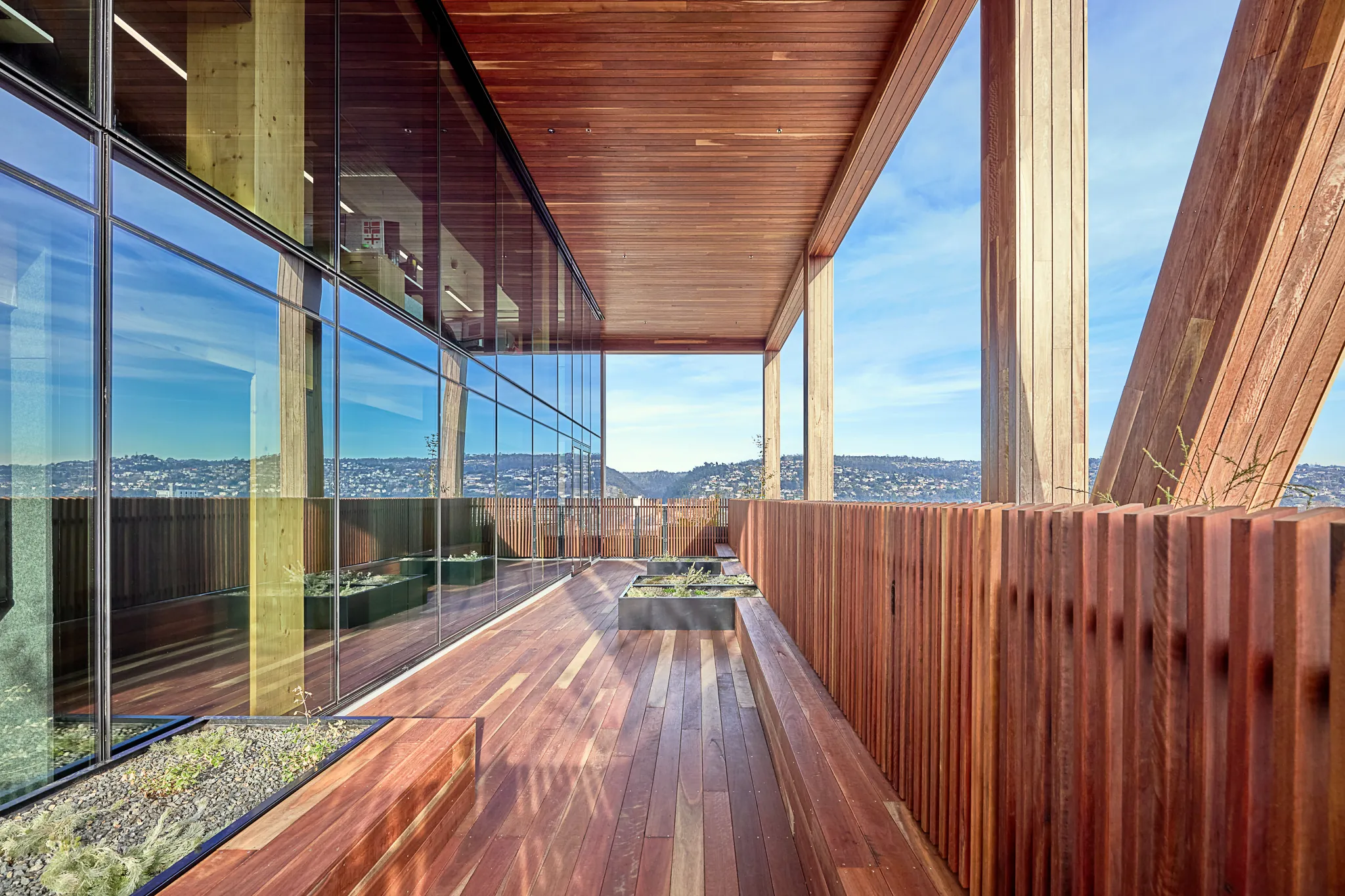